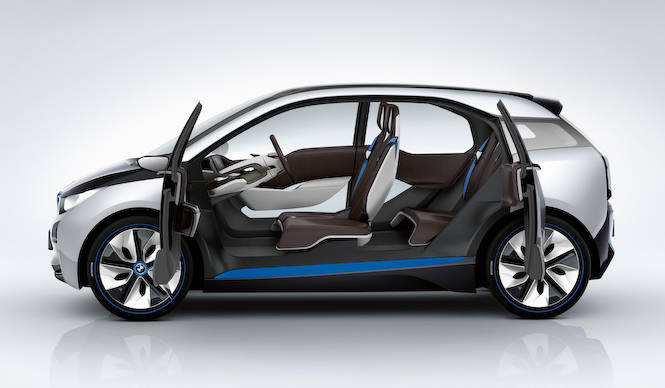
BMW初のEV - BMW i3 ができるまで|BMW
BMW i3|ビー・エム・ダブリュー i3
BMW初のEV
BMW i3 ができるまで
BMW初の市販電気乗車となる「BMW i3」がいよいよ、登場間近だ。BMWはなぜ、このクルマをつくるのか、そしてどうやって? ライプツィヒのBMW i工場から、渡辺敏史氏のリポート。
Text by WATANABE Toshifumi
EV時代で異業種がクルマをつくる説について
EVの時代になると部品点数は劇的に減り、既存の重厚長大な生産技術を要することもなくなり、結果として異業種からの自動車ビジネスへの参入が容易になる──という見解を耳にしたことのあるかたは多いとおもう。
もしそれが、完成車の開発から生産を含めた総合メーカーの仕事を指しているとすれば、これはまったく的を射ない話だ。
この業種が背負う莫大な社会的リスク、それにたいしての利益率の低さ……と勘定ベースだけでみても、いかに非効率な投資かが即座に理解できる。地場に猛烈な需要がある国ならいざ知らず、これほど労多くして実伴わない産業に今から賭そうなんて考える方が不自然。現場の真ん中にいる人々も、多くはそうおもっていることだろう。
いっぽうで、21世紀に入ってからの時代は、堰を切ったように変わりつつあることは間違いない。その変化に対応するために、自動車メーカーが収支的にも開発的にも純潔を守り通すことに限界を迎えつつあるのもまた確かだ。
かかわる人数や動く金の大きさから、傍目からみれば既得権益とも受け取られかねない自動車ビジネスの世界が、異業種との協業で相乗的発展を目指すという方向性を模索しはじめている。
つまりクルマ屋の側が、ビジネスパートナーとして見知らぬ世界との接触を積極的にはかろうとしているという現状がそこにあるわけだ。
自らのプロダクトが掲げるべき自我や責任と、求められるこの柔軟性とをどう折り合いづけるのか。それをいま、もっともリアルかつダイナミックにうかがうことができるのが、BMWの「i」プロジェクトなのだとおもう。
BMW i3|ビー・エム・ダブリュー i3
BMW初のEV
BMW i3 ができるまで (2)
Mとi
BMWの直轄としてスポーティネスを突き詰めたプロダクトを供する「M」にたいすれば、「i」は同様の位置づけでサステイナビリティを突き詰めたプロダクトを供することを主目的としている。
一見真反対の両者がBMWというハブに繋がるからには、社是である「駆けぬける歓び」を満たしたものであることが大前提だ。平たくいえばエレクトリック パワートレーンの普及を見据えた i に、歓びをもたらすものはなにかということになる。
i ブランドの本格的な展開は、恐らく今年のフランクフルトショーでプレミアとなる「BMW i3」がその皮切りとなる。それに先んじておこなわれたテクニカルワークショップでは、その答えが様々な形で用意されていた。
風が生み出すクルマ
舞台となったのはライプツィヒ工場。東西統一後のドイツにつくられた最新設備を備えるBMWの大型プラントは、i3の本格的な生産のための様々な準備が急ピッチで進められている。
敷地内に据えられた大型の風車は本格稼働の暁には計4基となり、アウトバーンからも臨めるシンボリックな存在となるはずだ。もちろんi3にとって、それは単なるランドマークではなくフィロソフィの一端をしめすものとして機能する。
BMWとしてははじめての専用設計EVとして開発されるi3の生産工程は、その環境性能をさらに後押しすべく、驚くほどのエネルギー削減が計画されている。
その象徴的な存在となる4基の風車は理想環境において、i3の生産にまつわる電力を100パーセント カバーするというから驚きだ。
もちろん背後には従来の電力供給ネットワークというバッファがあるものの、これほど自然エネルギーに大胆に依る自動車製造ラインは存在しなかった。
BMW i3|ビー・エム・ダブリュー i3
BMW初のEV
BMW i3 ができるまで (3)
クルマづくりの発想からちがう
もちろん、それはつくられる車両側の貢献から得られた結果でもある。
BMW i3は、シャシー側とボディ側とをそれぞれ「ドライブモジュール」、「ライフモジュール」と明確に区別する設計思想で構成されており、その素材は前者がアルミニウム、後者がカーボンでほぼ100パーセント構成されている。
つまり材料時点から普通のクルマとはまったくちがう発想でCO2の削減を織り込むことのできるエンジニアリングとなっているわけだ。
たとえばi3の場合、ドライブモジュールを構成するアルミニウムの50パーセントはアルミ缶などの再生素材を用いてつくられている。
そもそもアルミはボーキサイトからの精製時点で電気を大量に用いるいっぽうで、自動車にとっては軽量・高剛性を達成できる魅力があるわけだが、リサイクル比率を上げることによって初期の電気使用によるCO2排出量を大きく削ることができる。
BMWが i ブランドにおいて最大のテーマとしているサステイナビリティは、商品そのものの環境性能に留まらず、ライフサイクルアセスメントに基づいて鳥瞰的に図られていることも大きな特徴だ。
BMW i3|ビー・エム・ダブリュー i3
BMW初のEV
BMW i3 ができるまで (4)
地球を半周するカーボン
そしてライフモジュールと称される上屋は、カーボン材を用いてモノコックを構成することにより、生産工場での従来からの工程を排除することを可能にした。
ボディパネルはポリプロピレンのアウターパネルを直接染色することで塗装工程に必須だった水の使用量をほぼゼロにまで圧縮したほか、独自の熱間成型によってドライカーボンと同等の剛性と重量を達成しつつ生産性を飛躍的に高めたカーボンボディは、大量の電力を要する溶接工程を無としている。
EVであるi3にとって、軽さは航続距離を稼ぎ出すための、ことさら重要なポイントだ。
自動車の次世代素材の本命と目されるカーボンにBMWは早くから着目し、一部モデルのルーフパネルなどに用いることで生産や品質にかんするノウハウを蓄えてきた。
その知見を一気に開花させたi3のカーボンボディ生産工程は、じつに地球を半周以上という距離を経て形になっている。
日本の三菱レーヨンからBMWへ納入されるカーボン原糸がまず向かう先はアメリカだ。
ワシントン州郊外にあるモーゼス湖には、カーボン成型を得意とするドイツSGL社とBMWとが共同出資で設立した合弁会社の工場がある。
そこで原糸は焼結され繊維へと加工される。その繊維は大西洋を渡りドイツへ上陸。BMWのランツフート工場へと移送され、パネルへと成型される工程を経て、ライプツィヒ工場に納入、そこでアッセンブルされるという寸法だ。
この複雑なマイレージの理由を遡ってみれば、ランツフート工場はBMWの鋳造技術が集積しており、成型にたいする知見をもったスタッフやプラントがあることから、カーボンの加工にかんするBMWの中核になっている。
そしてアメリカでの繊維化工程は、湖による水力発電によりカーボンの焼結にまつわる膨大な電力を100パーセント賄えるというメリットがあるわけだ。
そして素材が軽いということは、移送にまつわるCO2の排出も低く抑えられるというメリットを生む。これほどの長距離を跨いでなお、水力発電の恩恵をしっかり享受できるというところに、自動車のマテリアルにおけるカーボン素材の先進性があるのかもしれない。
BMW i3|ビー・エム・ダブリュー i3
BMW初のEV
BMW i3 ができるまで (5)
BMW i3がおこすパラダイムシフト
「発動機」という言葉そのものを社名とするBMWは、言うまでもなく、内燃機関のパワーと効率、そして官能性において世界から高い評価を得てきたメーカーだ。
その会社が手掛ける電気の発動機を持つi3のディテールには、想像以上に自社内での技術開発が深く関与していることが見て取れる。
そのいっぽうで従来の自動車メーカーでは、あまりに縁遠い弱電や素材にかんする領域では、躊躇なく業界外と技術交流をおこなってきたことも充分にうかがえた。
いずれにせよ、今までとはまったくちがう発想の元に戦略を立て、開くべき扉から知見を招き入れなければ話がはじまらない。EVの本当の難しさは無責任な外野よりも、これまで散々苦悶をつづけた自動車メーカーの方がよく理解しているのだろう。