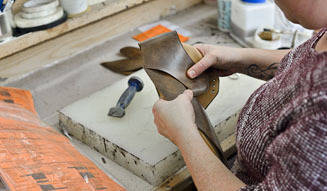
JOHN LOBB|最高のジョンロブの一足ができあがるまで(3)
JOHN LOBB|ジョンロブ
製造ラインを増設したファクトリーを完全取材~縫製から釣り込みへ~
最高の一足ができあがるまで(3)
今回のファクトリー取材では、ジョンロブの靴作りの一連の流れを紹介している。普段では見ることのできない革パーツや、作業工程を知ったあとで自分のジョンロブを手にとって見ると、さらに靴が愛おしく感じることだろう。さて3回目は、縫製セクションから、いよいよ靴作りのメインとなる“ラスティング=釣り込み”へと移っていく。
Text by KAJII Makoto (OPENERS)Photographs by ARAKI Ryuji
数字下2桁がラスト(木型)ができた年
靴作りにおけるもっとも重要な要素のひとつがラスト(木型)だ。OPENERSで掲載しているジョンロブの記事には、かならずラストの番号を記載しているので、そちらもご参照いただきたい。
ジョンロブの既製靴のラストはプラスチック製。その理由を聞くと、「湿度などの環境に左右されず、機械を通すものでもあるので、丈夫なプラスチックが一番」との答え。既製靴のサイズは5から12まであり、既存のラストでは、7000番が最も数が多いそうだ。
ラスト番号「8896」は1996年に作られたもの、「7000」は2000年製、イヤーモデルの「JOHN LOBB 2013」に使われている「2511」は、既製靴のラストでもっともあたらしい2011年製。
つまり、4桁の番号の下2桁が「ラストができた年」を示しているのだ。こういった豆知識で、靴選びが楽しくなるのだ。
最新マシンでの釣り込み
革の断裁セクションや縫製セクションの静かな雰囲気から一転、靴工場らしい音が聞こえてくる製造セクション。音は断続的に聞こえてくるが、接着剤の匂いなどはほとんどしない。
靴の製造において、もっとも重要な工程が“ラスティング=釣り込み”。底付けの第一段階で、中底を仮止めした靴型に、スティフナー(月型芯)を入れたアッパーをかぶせる。そしてアッパーの爪先の端を靴型に巻き込むように釣り込んで、中底のリブに止めていく。
ビスポークの靴作りとおなじく、スティフナーを湿らせて、ほどよい乾き具合にする手法をとっている。
ファクトリー拡張にともなって導入した最新マシンでは、イヤーモデル「JOHN LOBB 2013」のつま先をラスティング中。湿らせているスティフナーは柔らかいので、どんなかたちにも変えられるのが特徴だ。
革がデザインを記憶する
また、ジョンロブではアッパーの革とライニングが別々に仕込まれている。これは、「アッパーの革とライニングがそれぞれ独立して動くことが履き心地に直結」するからということで、「スーツも表地と裏地が分かれていることで、着心地の良さに影響するのとおなじ理論」だそうだ。これもビスポークの靴作りにみられるこだわりのひとつ。
ジョンロブの靴が高価だと言われる理由を挙げていくと限りがないが、このようなビスポークの工程を既製靴に取り入れていることや、インソールやスティフナーなど、見えない部分にもフルグレインの革を使っていることなどがある。
製造セクションにある使い込まれた機械では、別々になっているアッパーの革とライニング部分を引っ張って留める作業がおこなわれていた。ライニングを引っ張り、アッパーを引っ張って、ヒール部分をラスティングする一連の流れを見ていると、「トップラインってご存じですか? ジョンロブの靴を後ろから見るとヒールが包み込まれるようになっていますが、これは、フルグレインの革のスティフナーが形を覚えることで生まれるフォルムなのです」と教えてくれた。
靴の随所に贅たくにフルグレインの革を使う理由は、取材の1回目を参照してほしい。
そして、既製靴工場での作業は難しいとされる、ワイヤーでアッパーが緩くならないように留めている工程なども説明を受けた。製造ラインで靴をラッピングしている理由を聞くと、「ジョンロブの革は人間でいう素肌に近く、ゴミや脂を吸い込みやすいので、製造段階でしっかりカバーしている」とのこと。
製造セクションでは、スティフナーを乾かすために丸1日かけて寝かせている。
最高のジョンロブの一足ができあがるまで(4・最終回)につづく
ジョン ロブ ジャパン
Tel. 03-6267-6010
http://www.johnlobb.com/jp