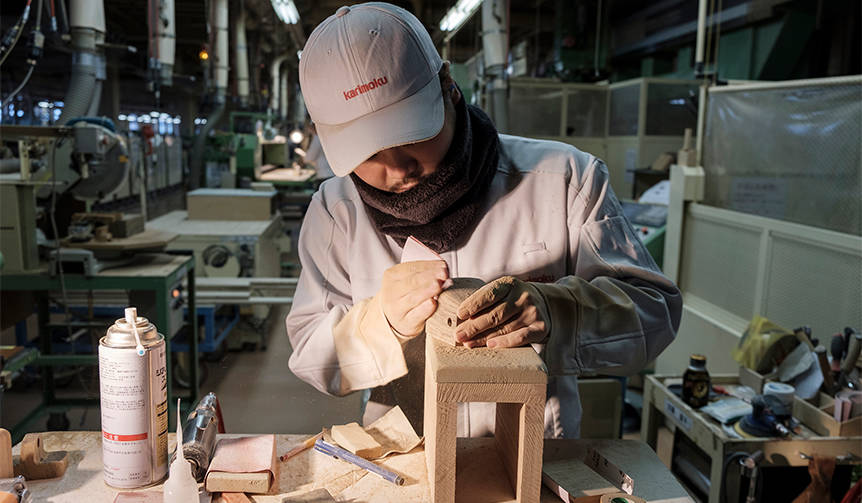
機械作業と人間の手作業を融合。キーワードは「ハイテク&ハイタッチ」|MEDICOM TOY
MEDICOM TOY|メディコム・トイ
カリモク ☓ BE@RBRICK 取材リポート 中編(1)
メディコム・トイとカリモクのコラボレーションで生まれた「カリモクBE@RBRICK」の製造工場を見学するため、愛知県知多郡東浦町にあるカリモク家具株式会社を訪れたOPENERS一行。今回はいよいよ工場で製造工程を見せていただくことに。ここでは木材の状態から職人の手によるさまざまな工程を経て加工され、塗装、組み立て、梱包まで行なわれているという。この日、製造していたのは2019年4月発売予定のBE@RBRICK × カリモク銘木シリーズ最新作「BE@RBRICK カリモク OVANGKOL 400%」。いったいどのようにしてBE@RBRICKとして命が吹き込まれるのだろう。
Photographs by OHTAKI KakuText by SHINNO Kunihiko
引き続きナビゲートしていただくのは、カリモク家具株式会社 マーケティングセンター 新規事業部の池田令和さん。最初に案内されたのは、胴体と脚部を加工する工程。機械作業と人間の手作業を融合させた生産ラインのキーワードは「ハイテク&ハイタッチ」だという。
※ ※ ※ ※ ※ ※ ※ ※
池田 それでは実際に製作工程をご覧ください。弊社には木製家具のさまざまな部品を加工するための機械が設備されており、それらを使ってBE@RBRICKの各パーツの形状ごとに最も効率よく作業できるよう工程を分けています。作業工程は家具作りと同じですが、小さいものの方が仕上げるのは難しいです。
ここは胴体と脚部を加工するところで、最初に機械で大まかな形にします。材料をどういう形に取るかを指定する作業を“けがく”と言うんですけれども、機械にかける前に前工程で荒取りして余計なところは先にとっておくんです。
腰や両脚のパーツは木目を揃えるため、なるべく近い場所の木を使うようにしています。
この作業でとても大事なのは、正面と後、どちらの面にどんな木目が出るかがここで決まるんです。どちらの木目が表に出たほうがきれいか決めるのはこの工程担当職人の裁量なので、非常にセンスが問われます。BE@RBRICKの工芸的価値を決める最初の分岐点はここです。
※ ※ ※ ※ ※ ※ ※ ※
加工した時点で節が出たり、穴が空いていたなど社内基準に適合しないものは、その時点で次の工程に回さず、ストックの木材と交換してもらうとのこと。目に見える情報だけで瞬時に判断していく才能は職人さんの経験の賜物だ。
※ ※ ※ ※ ※ ※ ※ ※
池田 職人がスタートボタンを押すと、ここから機械が刃物で形作っていきます。切断加工の多いパーツも一時的に木ネジで止めてあるので、刃物の負荷がかかっても飛んでいくことはありません。
止めておいた穴は組み立てると隠れてしまう部分。製品の出来栄えを上げるには、いかなる工夫もする、というのが私どもの考えです。
加工機械から上がってきた時点ではまだ角(カド)がたくさん立っているんですが、それらを紙ヤスリで一定に潰したり、メディコム・トイさんから指示されたアール(角を丸めて円弧状に加工した状態)にしていくのは、すべて職人の手作業でやっています。
機械と人間の手作業の最適なハイブリッドを、私どもでは「ハイテク&ハイタッチ」と呼んでいます。
これは家具を作るときに用いる言葉で、そのままBE@RBRICKを作る際にも使っています。寸法を切り揃えることは機械に任せて、そうではない部分──こういったBE@RBRICKの顔や手脚のような曲面のフィニッシュは、やはり人間の目と手の感覚でやったほうが抜け漏れなくきれいに仕上がるんです。
また機械から出たまま組み合わせると、BE@RBRICKを立てたときにどうしても左右の脚の高さが微妙に揃いません。これを“ガタ”といいます。そのガタをなくす作業も彼の仕事です。これをやらないまま塗装工程に行くと取り返しがつかないので、このレベルは非常に精度が求められる仕事です。
腰と脚にはお客さまに見えなくなる部分に番号がふってあって、この後の工程も全部つながっているので、ここでガタがなければ、製品になってもガタがないということです。
職人たちは「治具(ジグ)」といって、BE@RBRICKの各パーツに合わせて形をとったり、バランスを見たり、
自分たちでチェックするための道具をいろいろ工夫して作り出して使っています。
作業者からここが不満だ、もっと効率よくできる方法はないかという声が上がると、新たな治具を考える担当が改善する。そうやって、どんどんバージョンが上がっていくんです。
※ ※ ※ ※ ※ ※ ※ ※
職人さんに話をうかがったところ、1日の工程で仕上げられるのはわずか15体程度。いかに神経を使って作られているかが分かる。ひとつの工程が終わると、また次の作業へ。一連の作業が最もやりやすいように配置されたレイアウトも職人の個性である。
Page02. 家具と同じクオリティを満たすものでないと世に出さない
MEDICOM TOY|メディコム・トイ
カリモク ☓ BE@RBRICK 取材リポート 中編(2)
家具と同じクオリティを満たすものでないと世に出さない
続いて頭部を加工する現場へ。ここでは先ほどと異なる巨大な機械が待ち構えていた。
※ ※ ※ ※ ※ ※ ※ ※
池田 頭部は、平面がまったくない3D曲面のため特に加工が難しいんです。
最初に“荒取り”と言って頭に近い形に木材を切っておいてから、機械にかけます。これはカービングマシンといって、グリップでキャッチした木材をいろいろな角度から回転させながら刃物に当てて立体物を作ることができる機械です。山の等高線と一緒で、ちょっとずつ、ちょっとずつ削って形を作っていきます。
この機械の面白い特徴として、4個あるグリップの1番手前に例えばコーラの瓶をセッティングして縁をなぞると、連動して他もみんな同じ動きをするんです。つまり同時に4個、
まったく同じ形に削ることができるということです。今回は既にプログラムデータを入れているので、出力だけでBE@RBRICKの頭部が4個同時に加工できます。
この機械はダイニングチェアなどに使う複雑なデザインの脚の加工のために導入された機械なんですけれども、首の部分を残しておいてグリップで挟めば頭部を複数同時に量産できるということに気がつきました。
おやっ? と思うかもしれませんが、作っている段階ではBE@RBRICKに首があるんです。要は機械でキャッチするための部分を残しておいて、最後にそれを削除して胴体とつなぎます。
機械から上がってきた材料はリム(ふちの部分)が残っていますが、これもすべて手でなぞって取り除きます。ここからは人間の手作業で、ひたすらどれだけきれいなアールを作っていくかが問われます。
ちょっと、ほっぺたを触ってみてください。機械から上がったばかりのものはザラザラですが、これを職人が調整するとツルツルになります。ハイテクである程度のところまで近づけて、
ハイタッチでここまで持っていく。カリモクが常に目指すクオリティです。
※ ※ ※ ※ ※ ※ ※ ※
担当職人にうかがうと、樹種によって多少の違いはあるが、機械から取り出した状態からひとつあたり約30分ひたすら磨いてようやく商品になる品質になるという。柔らかい木は形が崩れやすいので硬い木の方がやりやすいと聞いて、なるほどと納得。中でも一番神経を使うのは「鼻」。鼻を大事にするように言われており、形が崩れてしまわないよう特に念を入れて丁寧に仕上げているそうだ。そしてパーツが完成すると、いよいよ塗装工程へ。木肌の風合いはそのままに、家具クオリティで仕上げられていく。
※ ※ ※ ※ ※ ※ ※ ※
池田 塗装工程とパーツの組み付けはここに集約されています。まず、左脚の内側にカリモクのロゴを入れた後、塗装に入ります。昔は焼印を入れてましたが、2016年の終わりからレーザー機を導入したので現在はレーザーで刻印しています。
BE@RBRICKは木の風合いを楽しんでいただくため色をつけないものが多いのですが、保護用の被膜として家具と同じく透明のウレタン塗装をしています。カリモクでは家具の塗装はおおよそ9工程ですが、BE@RBRICKはそのうちの大事な5工程から6工程、つまり着色以外は家具とほぼ同じ工程、品質で仕上げています。
通常の生活レベルであれば、水をこぼしても染みになることはありません。
被膜ができているので湿度を吸って割れることも起きにくい状態になっています。そこまでしなくてもいいよという声もあるかと思いますが、カリモクとしては家具と同じクオリティを満たすものでないと世に出さないと決めているので、頑なに守っているところです。
中には特殊な塗装をしたモデルもあります。例えば、ジーンズなどに使われる藍染めのインディゴ塗装を施したもの。それからクラック塗装という、ちょっと変わったものもあります。これは表面にクラック(割れ)ができた状態にする塗装です。
クラック塗装はまず下地の色を塗り、その上から乾燥すると収縮する塗料を塗って割れが出るようにしたものです。
湿度、温度、塗料の分量によって割れ方が違ってくるので、どうしても個体差が出てくるんですけれども、組み合わせたときに均一になるように、割れが大きいものは大きいもの同士、小さいものは小さいもの同士で合わせています。
またクラック塗装をアレンジした白樺風塗装というモデルも作りました。
これはもともとメディコム・トイさんから白樺の木で作れませんかという提案をいただいたんですが、白樺の木材は、弊社では通常取り扱いのない樹種なので、「代わりに白樺風の塗装なら、多分表現できますよ」と提案したところ、それで行きましょうということになったものです。fragmentdesignさんのモデルは木彫りのクマのような真っ黒な墨をイメージした色にしてほしいという要望でしたので、満足のいく色になるまで何度も実験を重ねました。
通常の家具で使わない色は、塗料の配合や濃さを調整しながらイチから作ります。実際に板に塗ってみて、「この色はどうだろう?」「もっと深さが必要じゃないか?」など話し合いながら、色出しの試験を繰り返し、最終的な塗装仕様が決まります。
※ ※ ※ ※ ※ ※ ※ ※
製品が完成すると検品を経て、梱包工程へ。家具と同じクオリティのBE@RBRICKをユーザーの手元まで安全に届けるため、ここでもまた最新技術による工夫がされていた。
※ ※ ※ ※ ※ ※ ※ ※
池田 2年前まではブリスターというプラスチック製の包装材を使っていましたが、輸送の段階で落としたりすると製品が壊れてしまうので、現在はボールペンを刺しても穴が開かない特殊なフィルムで挟む形で中の個体を固定しています。このフィルムを使うようにしてから輸送事故はほとんど無くなりました。
※ ※ ※ ※ ※ ※ ※ ※
以上で工場見学は終了。最後に今回製造風景を見学したカリモク銘木シリーズの新作「BE@RBRICK カリモク OVANGKOL 400%」について池田さんから特徴を解説していただいた。なかなか手にできない希少材を使った数量限定の銘木シリーズ。樹種の成り立ちや魅力が分かれば、BE@RBRICKへの愛着がさらに湧くことだろう。
※ ※ ※ ※ ※ ※ ※ ※
池田 オバンコールは西アフリカ原産、マメ科の広葉樹で、堅くて丈夫なことから高級家具に使用される希少材です。木目には緑色がかった茶色の美しい縞模様が入っていて、家具以外にもアコースティックギターのサイド&バック材として活用されています。なので、ギターを嗜まれる方でしたら「自分の持っているギターに使っていると木と一緒だ!」「しかも、こんな塊で」と、興味を持っていただけると思います。ぜひ一度手にとって触っていただきたいです。
BE@RBRICK カリモク OVANGKOL 400%
大ヒット中のBE@RBRICK×カリモク銘木シリーズ最新作は、高級家具や高級ギターなどに使用される希少なオバンコール材を使用したモデル。全高約280mm。MEDICOM TOY PLUSにて数量限定販売。2019年4月20日(土)発売予定・13万8240円(税込)
発売元:メディコム・トイ
販売元:メディコム・トイ
BE@RBRICK TM & © 2001-2019 MEDICOM TOY CORPORATION. All rights reserved.
MEDICOM TOY PLUS
Tel.03-3479-5555